Project Objective
Transformers are essential components in nuclear power plants, impacting everything from plant safety to revenue generation. At our client’s facility in Texas, their 112 MVA auxiliary transformer faced challenges with moisture buildup in its paper insulation system. Excessive moisture can weaken the insulation and increase the risk of failure. To address this, Kinectrics used advanced low-frequency heating technology to dry the paper insulation effectively within the limited, planned outage period.
Project Scope
A comprehensive evaluation of the transformer’s initial condition was conducted, including a review of oil test reports, on-site inspections, and diagnostic electrical tests. The initial moisture content in the paper insulation system was estimated to be between 2.5% and 3.0%.
- Drying Process: To heat all of the internal components a large oil processor was used to recirculate hot oil throughout the transformer system. Following this, deep vacuum was applied to start the moisture extraction process. A low-frequency power source was connected to the transformer, and current was circulated through the winding conductors, generating heat within the windings and the paper insulation. Alternating cycles of LFH heating and deep vacuum drove moisture from windings. Moisture extraction was monitored in real-time throughout this process.
- Final Steps: After a suitable hold period, a dewpoint measurement on the gas space in the transformer confirmed adequate dryness. The transformer was then refilled under vacuum with processed oil, followed by a final hot oil recirculation, oil sampling, and electrical testing to ensure readiness for return to service.
Value-Added Results
This dry-out method effectively restored the transformer’s insulation integrity by reducing the moisture level in the paper to less than 1% from an initial value of 2.5%. This level of dryness is significantly lower than could be achieved using alternative drying technologies in the allowed outage window. The entire dry-out cycle was completed in only eight days, resulting in minimal downtime. Traditional drying methods, by comparison, can take weeks or months to achieve this level of dryness. LFH drying is the fastest field-deployable processing methodology for achieving superior dryness results.
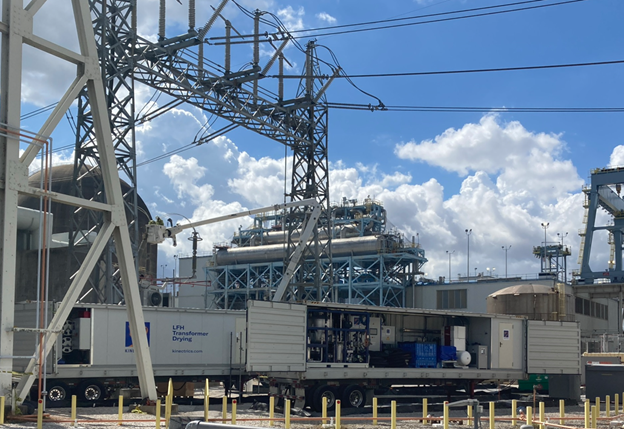