Overview
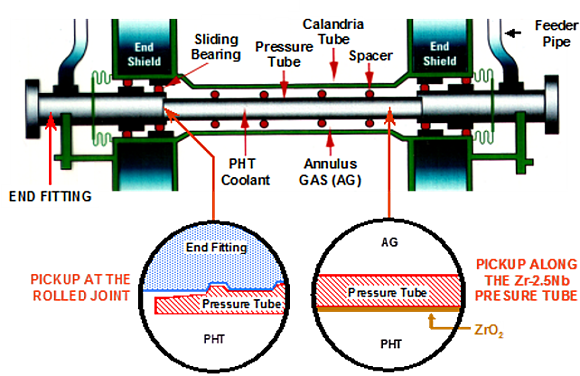
Pressure tubes are life-limiting components for CANDU nuclear reactors. Knowing the material condition of pressure tubes is critical to ensuring that they continue to operate well within their operating margin and design life. Confirmation of component aging is also critical to the maintenance of regulatory compliance and public confidence.
The Zirconium pressure tubes used in CANDU are susceptible to delayed hydride cracking (DHC). This phenomenon is caused by hydrides forming at crack tips, embrittling that region so that it fails under the stress and the crack grows. The hydrides themselves are made possible by enhanced hydrogen levels that arise as zirconium absorbs hydrogen in the reactor environment.
We have been working on pressure tube issues and DHC for decades enabling us to build a significant wealth of knowledge on the subject. Our expert team benefits from access to our in-house advanced test facilities which enable them to perform research and development into various degradation mechanisms associated with the Zr-2.5Nb pressure tubes used in CANDU reactors.
Why Us?
-
70 Years of Experience
We have been performing research and development on the Zr-2.5Nb (zirconium) pressure tube material used in CANDU reactors for over 70 years and have developed a considerable wealth of knowledge about how it performs in its working environment. We use that knowledge to resolve arising issues.
-
Up to Date and Relevant
Our experts actively participate as subject matter experts and key participants in industry committees that assist in the development of standards, most notably CSA N285.8 and N285.4. This work ensures that we are always up to date with the state of knowledge and of regulatory expectations.
-
Global Recognition
The in-depth understanding and comprehensive knowledge of the various degradation conditions CANDU pressure tubes can experience that we have developed is recognized by CANDU operators and their regulators around the world.
-
Advanced Test Facility
By continually investing in our advanced facilities we are to investigate and disposition emerging industry issues and respond to changing regulatory requirements. We are the trusted source for research in this unique field.
Technical Abilities
Hydriding Facility
Our hydriding facility enables us to simulate the hydrogen concentration in a pressure tube after years of service. It is an invaluable tool that provides us with the capability to deposit a hydride layer on both the inside diameter and the outside diameter of pressure tube sections up to 20-inch long.

Machining Facility
In-house machining facilities and precision machining procedures give us the capacity to machine many different types of specially designed specimens from transverse or axial directions of irradiated and unirradiated pressure tube sections. Examples of the specimens we can produce include, transverse and longitudinal tensile specimens, radial and axial delayed hydride cracking specimens, fatigue test specimens, and curved compact toughness specimens.
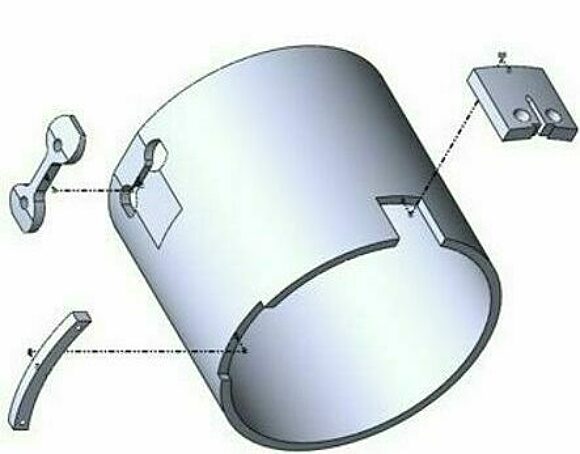
Large-Scale Delayed Hydride Cracking Initiation Test Facility
Because Zirconium pressure tubes are susceptible to delayed hydride cracking (DHC) understanding the condition of aging pressure tubes is critical to maintaining safe operating margins and regulatory operating approvals.
Our advanced test facility is used to study crack initiation behavior at the tip of simulated service-induced flaws by conducting DHC experiments on large numbers of hydrided zirconium pressure tube specimens. We conduct many tests in parallel in order to simulate reactor pressure and temperature operating conditions and generate experimental data, insights, and understanding that enable us to develop the analytical models and engineering procedures for DHC evaluation of in-service flaws in CANDU reactors.
This test facility is used to perform experiments on pressure tube specimens containing pre-cracks to measure KIH, a critical material property defined as the threshold stress intensity factor for DHC initiation from a crack under isothermal or thermal cycling conditions. It can also be used to measure the DHC growth rate in both radial and axial directions at different temperatures.
With thousands of experiments successfully designed and performed, we have developed a considerable knowledge of CANDU fuel channel material conditions.

Overload Test Facility
Flaw-tip hydrides that are present at the service-induced flaws in CANDU pressure tubes can be subjected to Service Level A or Service Level B overload. Overload is defined as a situation where the flaw tip hydrides are subjected to a stress higher than the hydride formation stress.
Overload tests determine the fracture stress on the notch-tip hydrides by applying increasing loads. This important information and its associated analysis is used to confirm the structural integrity of the CANDU pressure tubes. Our test facility can perform overload experiments on pressure tube specimens containing notch-tip hydrides formed at simulated service-induced flaws. This helps us to answer your questions about the cracking process associated and the aging condition of components.
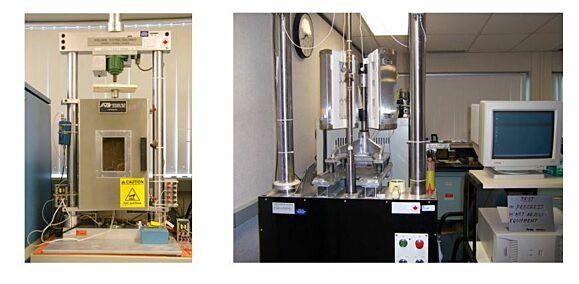
Tensile, Fatigue and Fracture Toughness Facility
An understanding of the transverse tensile strength, fatigue properties, and fracture toughness of zirconium pressure tubes is needed to inform nuclear operators and regulators about the component condition during reactor operation and provide assurance that ongoing operation is safe. Our specialized test facility is used to generate experimental data through the performance of tensile tests, fatigue crack initiation and growth experiments, as well as fracture toughness experiments. It is used for zirconium pressure tube specimens and specimens fabricated from other materials.

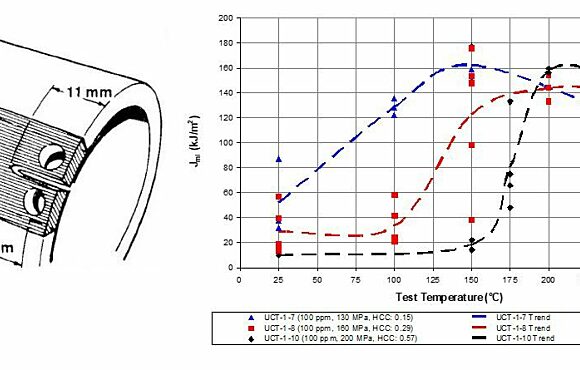
Pressure Tube Burst Test Facility
Pressure tubes must continue to operate within their design margins under both normal operating and accident conditions Our facility can be used to investigate the structural integrity of components and their ability to withstand deformation and fracture under extreme conditions. It enables us to pre-condition a full-scale burst test specimen and replicate stress and thermal cycles to form reoriented hydrides. These tests are followed by fatigue pre-cracking, and rising pressure burst tests, in order to measure the burst test fracture toughness.
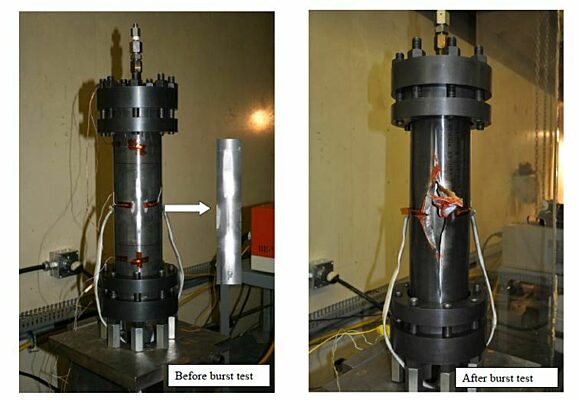
Post-Test Examinations
Our in-house scientists supported by specialized equipment leads to high-integrity post-test examination results. Our specialized equipment includes stereo microscopes, optical microscopes and a Scanning Electron Microscope.
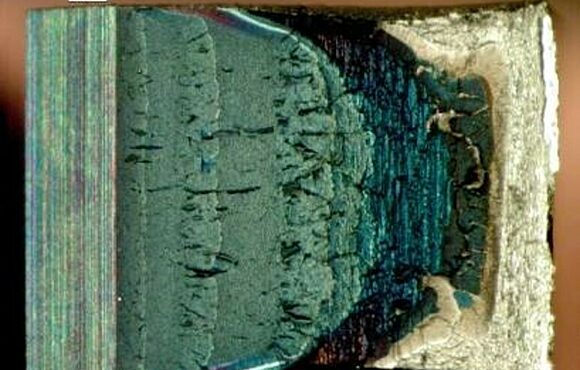
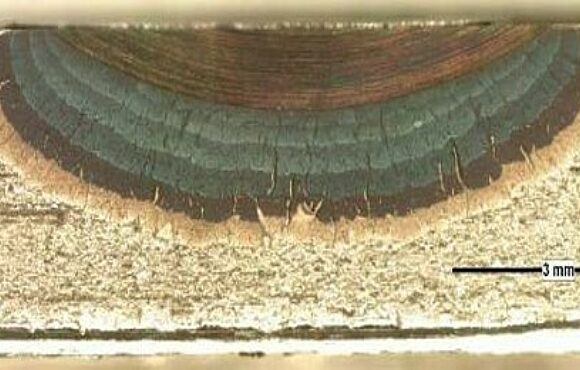

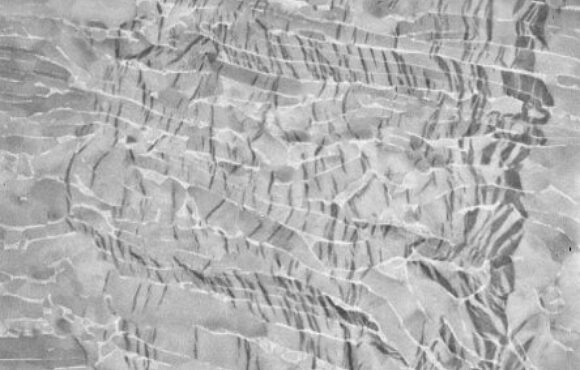
Our Proven Experience
Quality Assurance & Technical Standards
- ASTM E08 Committee
- Committee E08 on Fatigue and Fracture
- CSA N285.4 (2019)
- Periodic inspection of CANDU nuclear power plant components
- CSA N285.8 (2015)
- Technical requirements for in-service evaluation of zirconium alloy pressure tubes in CANDU reactors
- ISO 9001
- Quality Management System