Environmental Qualification Overview
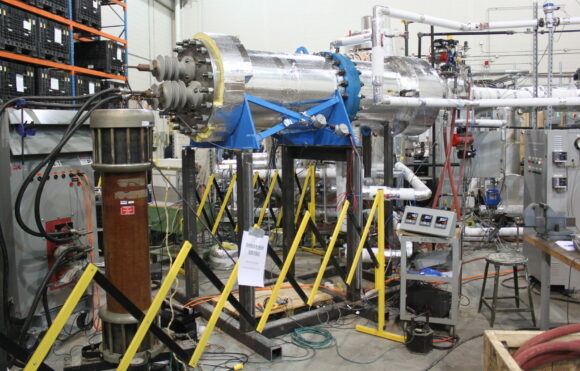
Environmental Qualification (EQ) is the process by which asset owners ensure that the safety-related equipment they use is compatible with normal operation and design basis accident environments throughout its qualified operating life. It typically includes accelerated aging (thermal, radiation, vibration, mechanical) tests, followed by seismic qualification and tests that simulate design basis accident conditions such as in Loss of Coolant Accidents (LOCA), High Energy Line Breaks (HELB), and Severe Accidents (SA). The testing must also cover any other condition or combination of conditions that the component may have to operate in during design and beyond-design circumstances.
Our experienced team can help you perform any required environmental qualification services, from the development of initial requirements and plans, through to the execution of comprehensive test programs.
Why Our Environmental Qualification?
-
A Comprehensive Trouble-free Package
We plan and execute all the environmental tests in our in-house facilities and then prepare reports that are provided in one comprehensive trouble-free package, with the minimum of test specimen transportation and handling.
-
World-Class Testing Facilities
Our laboratories enable us to perform thermal, mechanical, vibration, mild and harsh environment, electromagnetic compatibility (EMC), and electromagnetic interference (EMI) tests as well as seismic qualification and any other special environmental, seismic or functional tests you may need.
-
Reliable Results
Decades of experience enable our team to plan and execute the tests correctly so that they reduce anomalies, minimize rework and provide reliable results that build owner and regulator confidence.
-
The Tests you Need
A matrix approach allows us to bring together licensing, materials, testing, and other experts to develop the environmental tests that you need to determine the life of your equipment.
Our Environmental Qualification Technical Abilities
Our Approach
Every environmental qualification (EQ) test program is different, but the general process is always the same. Our experience enables us to appreciate the requirements and processes needed to execute EQ testing for a broad range of components. This includes developing the specific functional test requirements and the acceptance criteria and then providing the calibrated measurements. Our comprehensive facilities enable us to undertake a comprehensive range of tests enabling us to offer a one-stop shop service for all your EQ needs including:
- Thermal Aging
- Accelerated Thermal Aging
- Vibration
- Cyclic Aging
- Mechanical Aging
- Radiation Aging
- EMC/EMI
- Seismic
- Mild Environment
- Harsh Environment (LOCA/HELB)
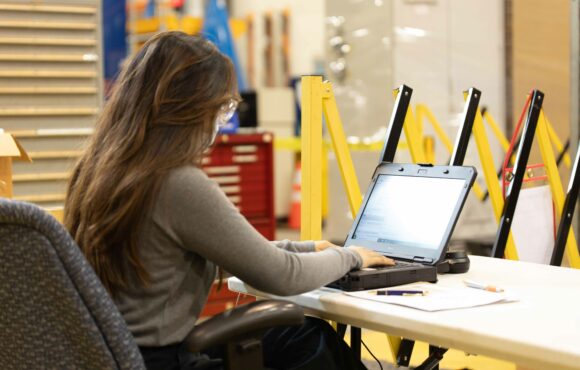
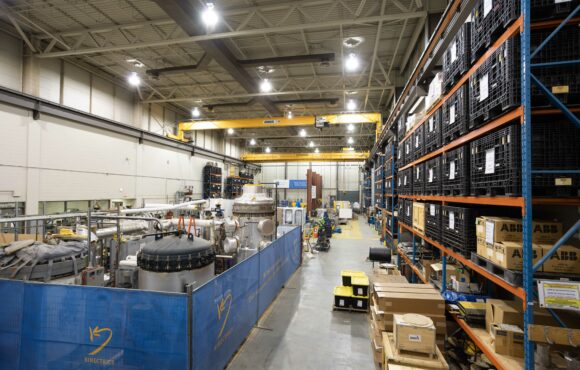
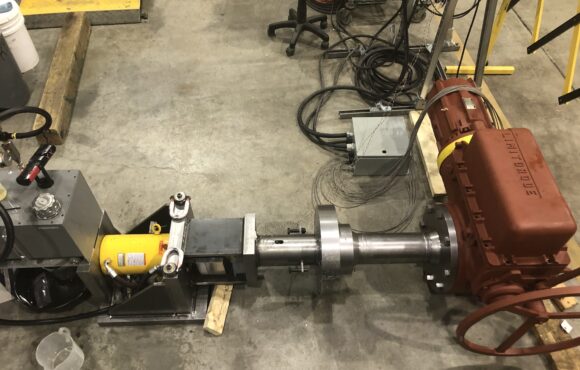
Qualification Planning
Qualification planning uses the requirements of 10 CFR 50.49, Reg. Guide 1.89, SRP 3.11, IEEE 323, CSA N290.13, RCC-E, NPP specifications, original equipment manufacturer specifications, and other applicable test standards to establish the EQ program. We use qualification planning to provide the most efficient EQ process which can include:
- Appropriate selection of representative test specimens
- Identification of significant aging mechanisms
- Identification of critical performance requirements and acceptance criteria
- Identification of EQ-sensitive materials
- Determination of normal and abnormal environmental conditions
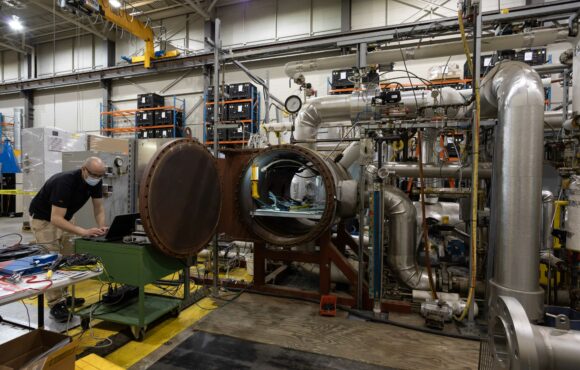
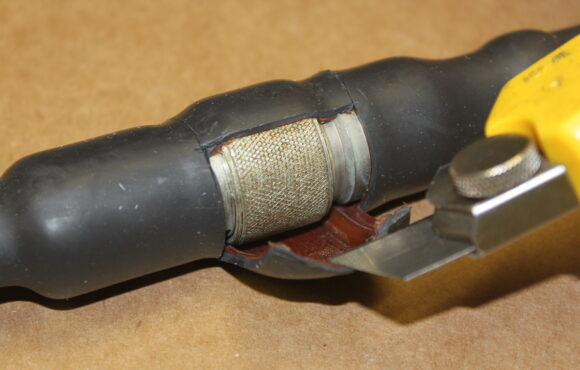
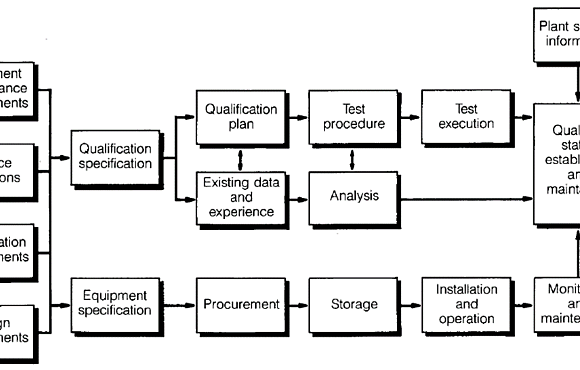
Technical Expertise
A successful qualification program needs to be supported by technical experts in various fields to ensure the adequacy of the test set-up, address any anomalies, troubleshoot any arising issues, and analyze the test results. We draw from our extensive in-house capabilities to support our EQ testing programs including:
- Transmission and Distribution Technologies for specialized electrical components (i.e medium voltage cables, transformers, etc.)
- Materials and Major Components for support from metallurgists, elastomer experts, and forensic investigations
- Analytical Chemistry for manufacturing of chemicals for spray and/or submergence, material analysis, and verification
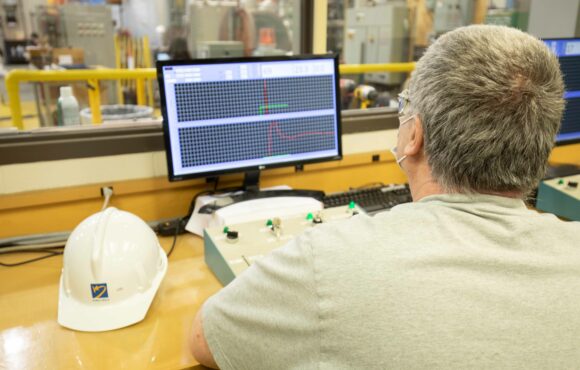
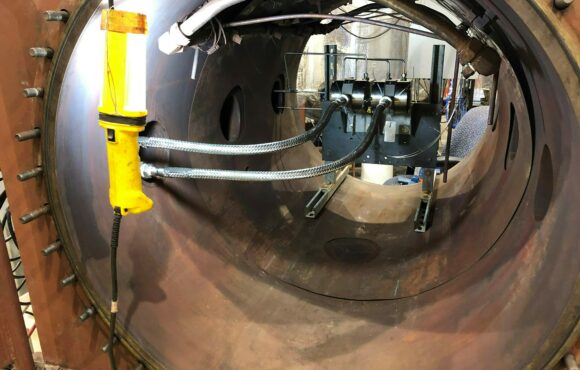
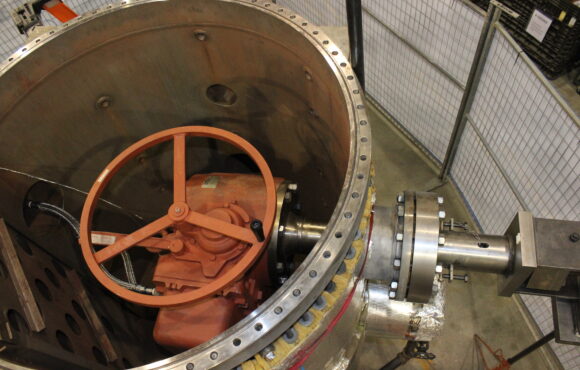
Test Execution
Our test engineers and technicians use the experience they have gained from qualifying virtually every type of component typically installed in nuclear facilities to:
- Carry out functional test design to verify component safety functions
- Use state-of-the-art data acquisition
- Select the best test instrumentation and metrology
- Test fixture designs (mechanical cycling, seismic, DBE)
- Use a rigorous Quality Assurance Program
- Apply appropriate specimen handling and foreign material exclusion (FME)
- Simulate and monitor test specimen inputs, outputs, and other operational requirements (voltage, current, insulation resistance, pressure, flow)
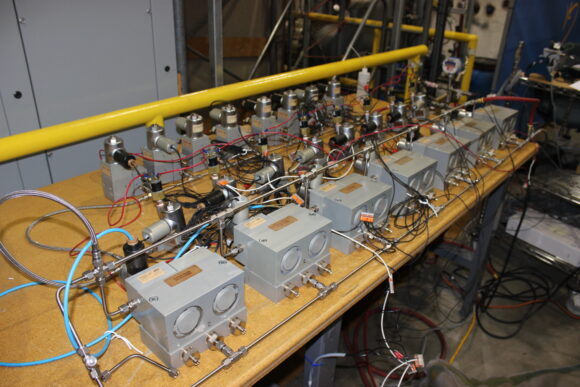
Our Proven Experience
Quality Assurance & Technical Standards
- 10CFR50 Appendix B (2021)
- Quality Assurance Criteria for Nuclear Power Plants and Fuel Reprocessing Plants
- ASME NQA-1 (2008)
- Quality Assurance Requirements for Nuclear Facility Applications
- CSA N285.4 (2019)
- Periodic inspection of CANDU nuclear power plant components
- CSA N290.13 (2018)
- Environmental Qualification of Equipment for CANDU Nuclear Power Plants
- IEC 60068-1
- Environmental Testing - Part 1: General and Guidance
- IEC/IEEE 60780-323 (2016)
- Nuclear facilities – Electrical equipment important to safety – Qualification
- IEC/IEEE 60980-344 (2020)
- Nuclear facilities – Equipment important to safety – Seismic qualification
- IEEE 317 (1983)
- IEEE Standard for Electrical Penetration Assemblies in Containment Structures for Nuclear Power Generating Stations
- IEEE 382 (2006)
- Standard for Qualification of Safety-Related Actuators for Nuclear Power Generating Stations
- IEEE 383 (2015)
- IEEE Standard for Qualifying Electric Cables and Splices for Nuclear Facilities
- IEEE Std 323
- IEEE Standard for Qualifying Class 1E Equipment for Nuclear Power Generating Stations
- ISO 9001
- Quality Management System
- ISO 17025 (2017)
- Testing & Calibration Laboratories