Overview
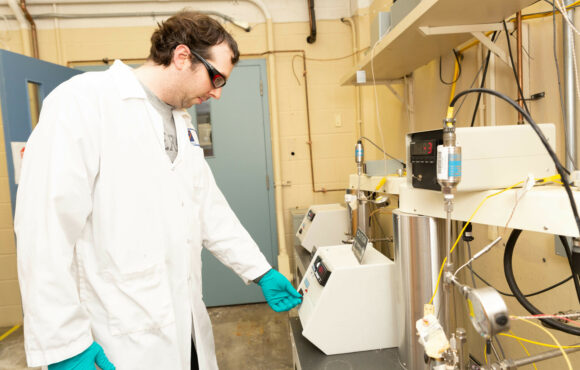
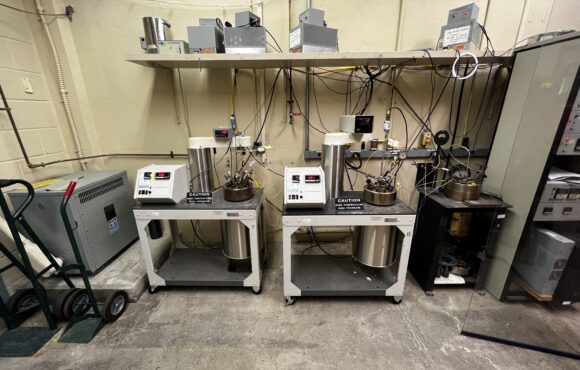
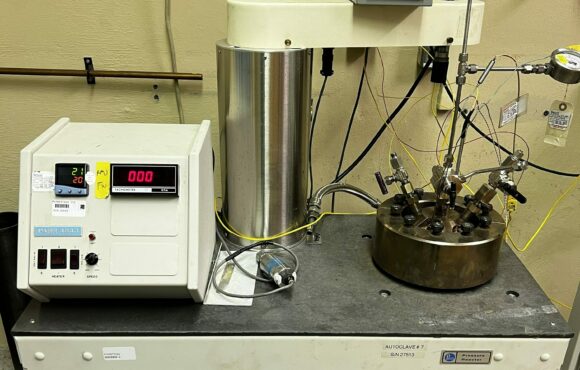
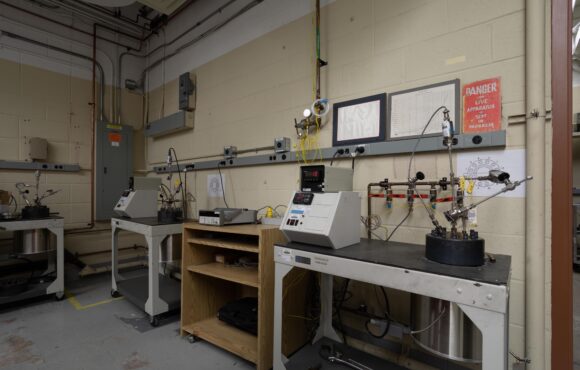
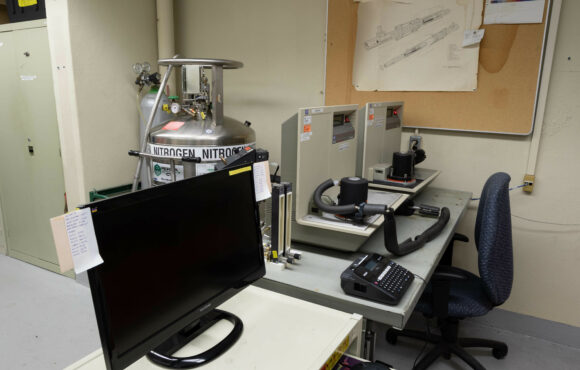
Corrosion is the gradual deterioration of materials (metals) by chemical or electrochemical reaction as a result of interaction with their surroundings. Corrosion testing simulates the environment in which a material will operate so that in-service rates of corrosion can be determined, materials can be selected, and design lives can be calculated. Many corrosion tests involve methods of accelerating the corrosion in order that results of this typically slow process can be obtained in a shorter period of time.
Corrosion testing is particularly important for components that cannot be inspected because they are inaccessible such as the components near the core of a nuclear reactor. Understanding corrosion rates is even more important in nuclear reactors because it not only leads to the loss of strength but the “crud” that arises can move around in the system and restrict flows while also potentially becoming activated and causing contamination.
Our corrosion testing capabilities have been developed over several decades of providing specialized technical support to the power industry and include methods of simulating reactor operating conditions. Testing can be conducted in an accelerated mode to deliver quick results and advance our understanding of corrosion-driven degradation mechanisms.
Why Us?
-
High Pressure, High Temperature Testing
A 7.5 liter autoclave that can reach a pressure of 1900PSI and a temperature of 350℃ and a 1.8 liter autoclave with a maximum pressure of 5,000PSI and maximum temperature of 500℃, enable us to simulate most reactor conditions.
-
Experts in the CANDU Reactor Environment
We are specialists in the materials used in CANDU reactors and their operating conditions, allowing us to quickly tailor tests for CANDU operators.
-
Experience-based Advice
Decades of experience enable our corrosion experts to quickly interpret test results, reliably project the progression of corrosion and provide experience-based advice on material selection.
-
Accelerated Tests
Our high-temperature and high-pressure test equipment make it possible for us to simulate environments and undertake accelerated corrosion tests.
Technical Abilities
Corrosion Specialties
Our corrosion group has decades of experience in fitness-for-service examinations of ex-service feeder tubes and steam generator components in support of CANDU major components periodic inspection and lifecycle management programs. We design and execute corrosion testing programs to determine end-of-life conditions and to test new materials and technologies.
The corrosion team has several years of experience conducting buried piping inspections and cathodic protection assessments at nuclear facilities. Our corrosion experts are qualified to NACE CIP Level 3 and can provide corrosion engineering consulting on:
- Buried piping inspection programs and execution,
- Corrosion control and asset integrity management (AIM) of critical components
- Cathodic protection design
- Electrochemistry in high-temperature high pressure aqueous systems
Our Proven Experience
Quality Assurance & Technical Standards
- ISO 9001
- Quality Management System