CANDU Fuel Channel Fitness-For-Service Solutions Overview
CANDU reactors contain several hundred fuel channels. Each fuel channel comprises a pressure tube, a calandria tube, end fittings, and spacers. They contain the fuel bundles and the primary coolant (heavy water) and as such are the heart of the reactor. During regular nuclear facility operation, the pressure tubes are exposed to high temperatures, high pressures, and intense radiation, which can cause them to deteriorate. CANDU operators must regularly monitor the condition of pressure tubes to ensure that they meet operational fitness standards. Subtle changes in shape, state of material properties, and the appearance of flaws must all be considered in establishing if they remain fit-for-purpose.
We are the industry leader in fuel channel engineering support and fuel channel fitness-for-service assessments, delivering a complete range of operational, lifecycle management, and refurbishment support to CANDU operators. Our team of experts have hundreds of years of combined experience that have led to the development of fuel channel fitness-for-service and lifecycle management practices that have been adopted across the entire industry.
Through our broad-based station support activities, proven leadership in research and development, and the development of new methodologies, we have maintained a keen awareness of current technical issues and regulatory sensitivities.
This diverse combination of experience and expertise has been instrumental in extending fuel channel life well beyond the initial conservative design limits.
Why Our CANDU Fuel Channel Fitness-For-Service Solutions?
-
Industry Leader
We are the industry leader for pressure tube integrity assessments and fuel channel engineering support, providing the peer-reviewed evaluations that enable the ongoing safe operation of national and international CANDU facilities.
-
Unique Abilities
As the developers, custodians, and sole users of industry-leading software tools we are uniquely able to carry out probabilistic evaluations of fracture protection, understand degradation mechanisms related to flaws, and complete leak-before-break (LBB) assessments.
-
Keeping CANDU Plants Operating
In the early 2000's we delivered a package of innovations that dispositioned the arising challenge of hydrogen-induced embrittlement enabling the CANDU fleet to continue operating.
-
Operational Experience
Many of our seasoned experts have spent years in former utility roles, where they were responsible for fuel channel lifecycle management and fitness-for-service programs.
-
Reputation
With 110 planned unit outages under our belt, we have developed a reputation for consistently delivering accurate fitness-for-service assessments to meet critical path restart timelines and regulatory commitments.
-
All Fuel Channel Work
Nuclear facilities rely on us to assist them with their fuel channel lifecycle management planning documents, to perform their component integrity assessments, and to assist with their regulatory submissions.
Our CANDU Fuel Channel Fitness-For-Service Technical Abilities
Outage Inspection Support
Outage schedules are tightly constrained in order to get the reactor back to producing power as quickly as possible. They are also designed to avoid costly delays.
We have a proven track record of performing challenging fuel channel fitness-for-service evaluations providing reliable results on time. With these evaluations in hand, you will have the confidence that the units can safely return to full power.
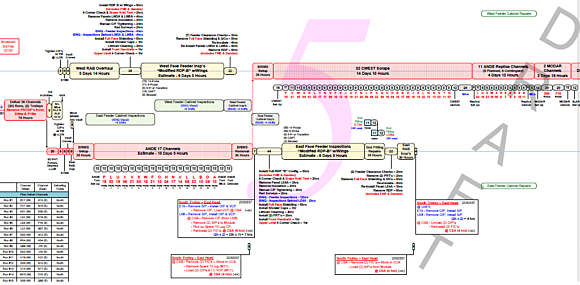
Engineering Evaluations
Using the results of fuel channel inspections, our experienced team can develop and improve the ability to predict material behavior to satisfy the requirements for periodic inspection and ensure compliance with the CSA N285.4 and 285.8 standards.
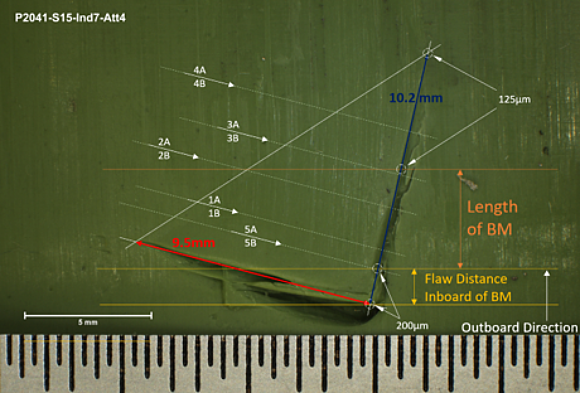
Leaders in Lifecycle Management
We are the leading authority when it comes to the CSA requirements for the in-service evaluation of pressure tubes. We authored the majority of the technical basis documents and underpinning content of CSA N285.8, at times under contract from the CANDU Owners Group (COG). Our staff chairs three of the four Fuel Channel Life Management (FCLM)-Joint Project Technical working groups, meaning our active involvement has resulted in the development of a solid technical basis to regain the operating safety margin and extend the operating life.
Additionally, we have developed the “road maps” for the execution of the joint projects, under which leading-edge, peer-reviewed fuel channel R&D is being performed to support extended operation. This participation and leadership provide us with unique insights into material behavior that we draw upon to support our customers.
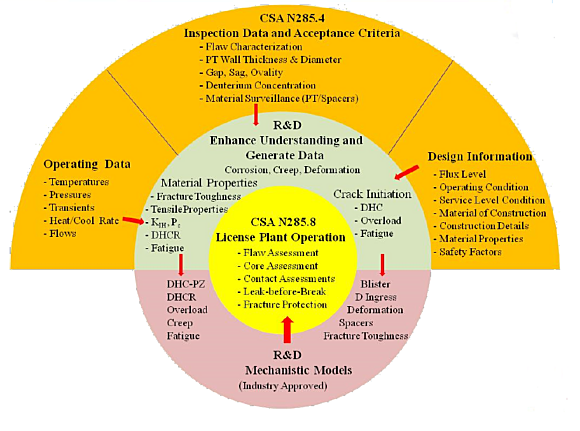
Maintenance Optimization
We help our clients optimize maintenance scopes by developing plans to ensure the right tasks are being performed on the right components at the right time. Our experts work to develop innovative solutions to determine what maintenance tasks are to be performed, on which components, and at what frequency to ensure fitness-for-service while minimizing costs. We work alongside your team to develop or improve methodologies to optimize necessary maintenance scope to meets outage plan targets and satisfy corresponding fitness-for-service requirements.
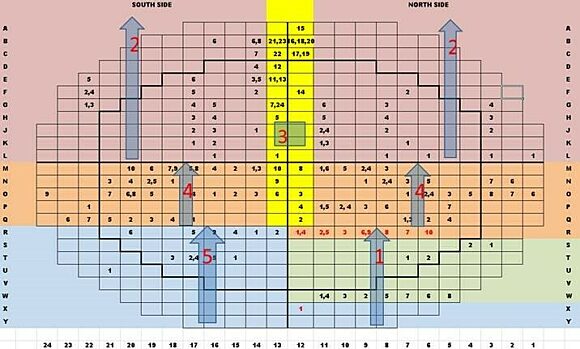
Our Proven Experience
Quality Assurance & Technical Standards
- CSA N285.4 (2019)
- Periodic inspection of CANDU nuclear power plant components
- CSA N285.8 (2015)
- Technical requirements for in-service evaluation of zirconium alloy pressure tubes in CANDU reactors
- CSA N286.7
- Quality assurance of analytical, scientific and design computer programs
Key Clients
Thank-you for your support with OPG’s P4S15 flaw disposition. I recognize the forensics, replica evaluation, analysis and modeling your organization performed and supported was crucial for us to demonstrate channel fitness-for-service. As a Team Lead, I heard you were instrumental in obtaining these results and I want to thank-you for the long hours you worked to expedite these results. This was an excellent example of collaboration between OPG and Kinectrics.