Overview
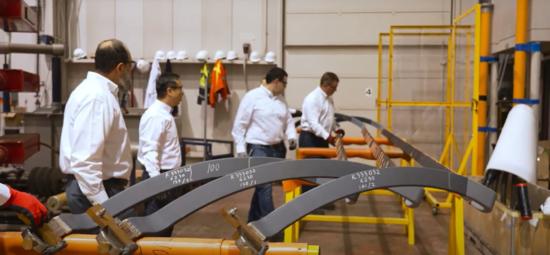
Understanding the condition of assets and identifying any age-related issues that could challenge the reliable operation of the equipment is at the heart of any lifecycle management approach for motors and generators. We apply expert knowledge and extensive testing capabilities to assess and quantify specific component degradation, the impacts on reliability, and the appropriate corrective or planned maintenance measures.
Our approach to generator and motor lifecycle management is to develop risk reduction programs that prevent unexpected events and extend the operating life of equipment. To enable this approach we provide cost-effective investigation and analysis. We conduct accelerated lifecycle testing and inspection services and we utilize our cradle-to-grave approach, backed up by comprehensive laboratory testing and field testing, to provide specialized consulting services.
The comprehensive visual inspection findings we perform, combined with detailed analysis of test results, provide the information needed to enable the best operational and commercial decisions to be made and to enhance asset performance.
Why Us?
-
Best-In-Class Services
By adhering to accepted industry test standards, we set ourselves apart from the competition and ensure our services are best-in-class. Our quality services include “on-time” schedule performance and superior reporting.
-
A History of Excellence
We are proud of our history when it comes to both client support and technical knowledge. Our specialized equipment and experienced personnel enable us to bring a new level of performance to your projects.
-
Independent Review
Because we are a third-party independent lab you will know that our assistance with rewind planning for high-voltage rotating machines, our analysis of stator bar and coil integrity, and our verifications of the design and manufacturing process quality can all be relied on.
-
Working With You
Our test and inspection plans begin with detailed client discussions. We take the time to understand the types of assets in service and their operating history and conditions and we take the time to review online data and confirm original equipment manufacturer recommendations and practices.
Technical Abilities
Confidence that Comes with Knowledge
Knowing how much life remains in stator bars and coils allows asset managers to obtain the maximum use from the existing windings. With this knowledge in hand, in-service failures can be prevented, the value of capital investments can be maximized, and long-lead planning can be put in place to minimize future costs and the time needed for maintenance or replacement of equipment.
As a third-party independent lab, we can assist with rewind planning for high voltage rotating machines, analyze stator bar and coil integrity, and verify the design and the manufacturing process quality.
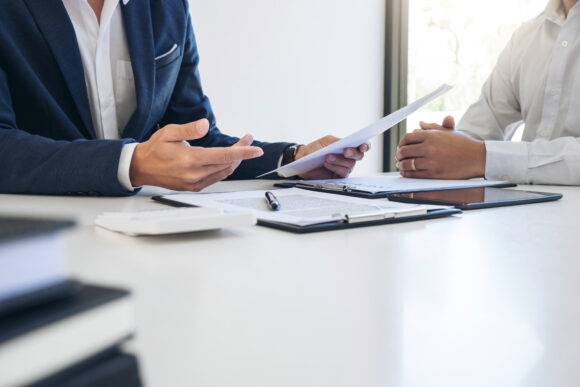
Quality Assurance of New Stator Bars and Coils
Partial discharge (PD) can occur if small voids are created within the insulation during manufacture, or air gaps occur between conductors at different voltage levels. Increases in PD activity over time have been shown to be indicative of advancing damage to the stator windings that could lead to premature failure.
Partial discharge testing is one of the most widely used methods to assess the quality of electrical insulation in new high voltage equipment.
When uprating a generator, newer materials and process can allow for less insulation and more copper. Uprate goals demand quality and uniformity of stator bar and coil production. Utilizing our PD testing will give you the confidence that partial discharge will not impact your asset’s life.
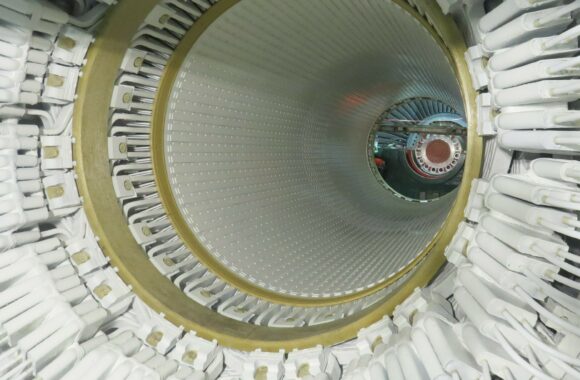
Preserving Asset Life
For the most part, high voltage generators and motors are reliable and do not require a lot of intrusive maintenance. But environmental conditions, hard starting requirements, structure vibration, and attention to excitation systems are all factors to be considered when it comes to a testing and inspection plan. And, depending on their duty or criticality, an asset management plan for scheduled monitoring and maintenance program may be needed if costly and unexpected loss of function is to be avoided.
Our test and inspection plans begin with detailed client discussions. We take the time to understand the types of assets in service and their operating history and conditions and we take the time to review on-line data and confirm OEM recommendations and practices. We then build and create a comprehensive inspection and test package to properly manage life expectancy and maximize asset value.
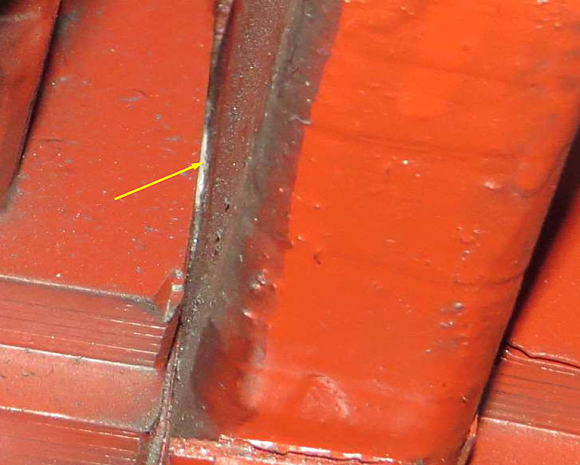
High Voltage Machines Field Inspections & Testing
Rotating equipment and electronics require regular inspection and maintenance, regardless of how often they are used or how long their operating hours are between maintenance. Supplementing regular maintenance programs with carefully planned inspections is imperative to ensure long-life and minimal down-time throughout the life of the generator assets.
We support existing specifications for performing tests and inspections in the field. Our team of experts can also work with industries and utilities to properly develop the best scheduled plan to ensure reliability, availability, and cost minimization.
With our years of experience and our breadth of knowledge, we support all original equipment manufacturers and their testing specifications:
- Generator Rotor Testing: Rotor Flux & RSO Test
- Insulation Resistance/Polarization Index (IEEE 43)
- Capacitance and Power Factor Tip Up (IEEE 286)
- DC Ramp Test (IEEE 95)
- Partial Discharge Testing
- TVA (Corona) Probe Tests (IEEE 1434)
- Generator Stator Core – EL CID
- BUMP Test
Expert Visual Inspections to Enhance Asset Life
The causes of non-performance in high voltage machines can often be found visually. The secret lies in having the knowledge and experience to know what to look for and where to look for it. Visual inspection can be a simple as a dusting, a search for small cracks and foreign debris, checking for looseness, rubbing, tears, missing objects or preexisting workmanship issues. Visual inspections need to be well documented, and the subtleties need to be carefully recorded to enable trend analysis. It is a discipline that requires the sort of expertise and know how that we deliver.
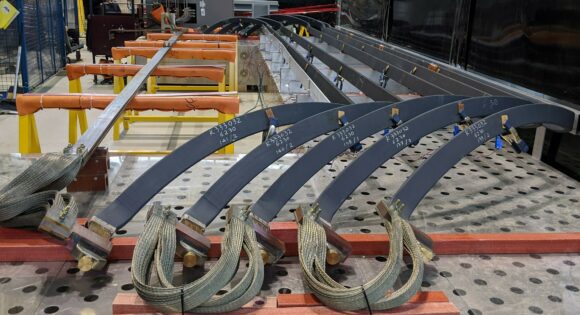
Full Complement of Testing Capabilities
Our expertise with all testing standards, applicable to both laboratory and field testing, ensures you are working with one of the leading testing resources for high voltage rotating machines. Our large laboratory of high voltage electrical test equipment supported by our experienced team, can bring many benefits to your inspection and maintenance program.
Testing and qualifying new stator bars is the best way to begin managing the lifecycle of high voltage generators or motors as it means any future field testing will have baseline data to generate keen insights and enable trending analysis. From product origin to end of life, our testing capability supports a full lifecycle management approach that will extend the operating life of your assets.
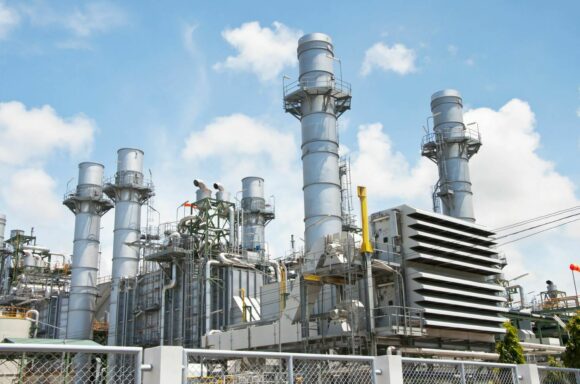
Expert Testing Capability
With our combined experience and capability of major original equipment manufacturer work, we go further, leveraging our independent status to add clarity and insights to our equipment lifecycle recommendations. We deliver analytical capabilities that go beyond the typical test and our inspection services provide reliable interpretation of the test results.
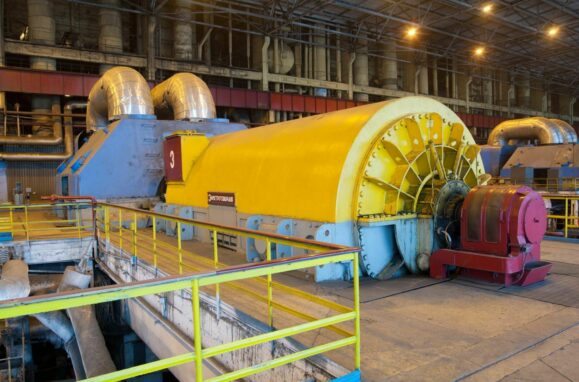
Comparative Database for Enhanced Analysis
The large number of tests we have performed over many years has led to us being able to draw on significant amounts of historical test data that we then use to provide you with clear informed insights. This level of analysis can lead to better understanding that may not be apparent from individual test results. This information can also be utilized to determine aging trends or partial discharge breakdown on comparable bars and coils.
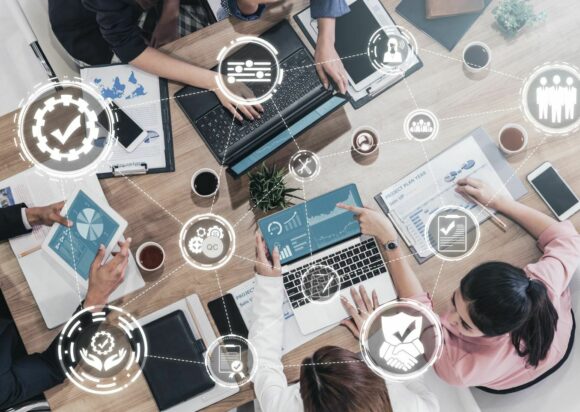
Enhanced Testing Capabilities
There is no one-size-fits-all approach when it comes to project scope in our business. Every equipment system has its own unique differences that require a proper tailor-made program to ensure all risks and potential issues are uncovered. From a single test on a small piece of equipment to a major test and inspection effort on a large project, we support and provide our testing services to manufacturers, utilities and prime contractors that includes enhanced site testing.
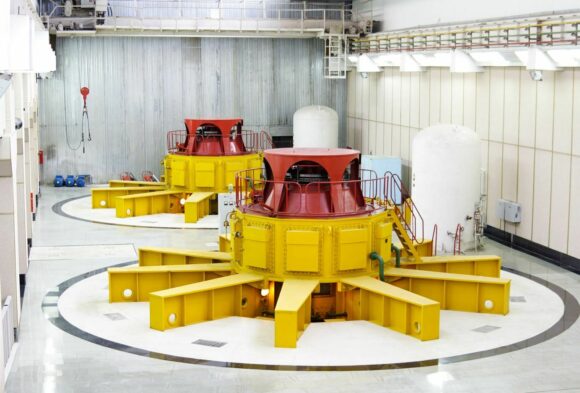
Getting to the Root of the Problem
Clients rely on us for forensic analysis of high voltage components. Our expertise in high voltage insulation, is the best available. If there has been a failure on a high voltage machine, our investigative and forensics work and laboratory analysis will provide the answers needed. Whether you want to deploy a pro-active program of asset testing and inspection or need a root cause analysis on failed components, we are ready to support your needs.
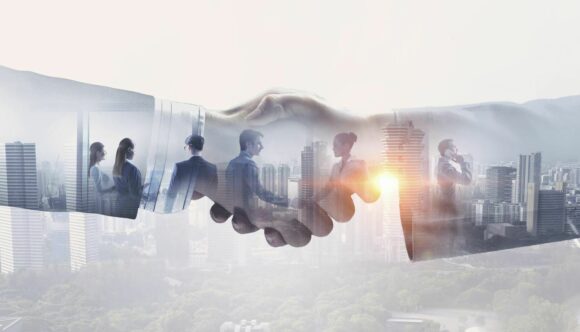
Our Proven Experience
Quality Assurance & Technical Standards
- IEEE 43 (2013)
- Insulation resistance and polarization index testing of stator and rotor windings
- IEEE 95 (2002)
- Recommended Practice for Insulation Testing - DC ramp test
- IEEE 286 (2000)
- Measurement of Power Factor Tip-up - Stator coil insulation
- IEEE 522 (2004)
- Testing Turn Insulation of form wound Bars and Coils
- IEEE 1043 (1996)
- Voltage Endurance Testing of form wound bars and coils.
- IEEE 1310 (2012)
- Thermal cycling of form wound bars and coils for large rotating machines.
- IEEE 1434 (2014)
- Test methods for measurement of Partial Discharges
- IEEE 1553 (2002)
- Voltage Endurance testing of form wound bars and coils for hydro generators.
- IEEE 1799 (2012)
- Detection of external discharges in form wound bars and coils - UV camera test
Key Clients
In addition to support from Generator OEMs we needed a third-party expert support group for independent machine assessments and decision making and to support both the development and execution of our internal Generator testing standards. Over many years, the Kinectrics Rotating Machines Group provided this expertise in a professional manner, with a strong focus on high quality and timely responses to both planned and forced outages.
It was our view that the most comprehensive condition assessment of Stator winding insulation, for aged machines, involved both AC and DC insulation diagnostics and High Voltage testing. Kinectrics was the only third-party expert group with the capability to provide the specific testing program required, resulting in a strong basis to declare ‘fit for continued service’ and recommendations for generator life extension decisions and planning