Overview
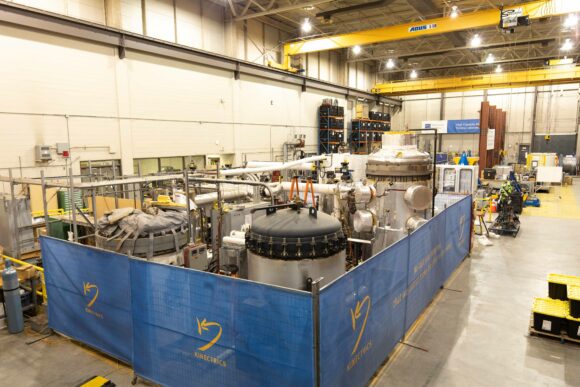
Component testing is often utilized to help ensure the equipment will meet its intended performance under normal operating conditions and in design basis, and other beyond design basis scenarios. Many of the tests are required by regulators to demonstrate operational safety.
With extensive nuclear experience, our team of experts can work with you to develop and execute the right-sized test plans that ensure safety and performance requirements are met.
Our nuclear facilities include:
- A Dedicated Loss of Coolant Accident Rig
- Environmental Testing Chambers
- Shaker Tables for Seismic Testing
- A Burst Test Rig
- Autoclaves for Corrosion Tests
- An Irradiated Materials Testing Facility
Why Us?
-
Customized Testing to Meet Your Needs
Our industry experts will work with you to identify the required tests and the best way to execute them or will recommend alternative solutions and approaches that will achieve your objectives. We also advise on the results.
-
One-Stop-Shop for Testing
In our wide variety of testing facilities, we are able to test entire systems, individual components, cables, electrical penetrations, valves, instrumentation, and all types of electrical and mechanical equipment.
-
Regulatory Knowledge
We have worked with regulators around the world so that we can help you develop the most effective and efficient test program no matter where your project is based.
-
Accuracy and Control
State-of-the-art and custom-designed equipment are operated by our skilled technicians and engineers, to ensure that you get precise and accurate results.
-
Responsive and Timely
If emergent issues arise we will use our broad range of in-house subject matter experts to support the quick turnaround times that will meet your needs.
-
The Specialist Tests You Need
In addition to the standard tests, we offer essential specialist tests that include loss of coolant accident (LOCA) tests and burst tests for steam generator and feeder tubes.
Technical Abilities
Loss of Coolant Accident Testing
Our Loss of Coolant Accident (LOCA) test facility can supply superheated steam at temperatures of up to 500 degrees Fahrenheit and pressures up to 150 PSI. It has the capability to provide chemical spray, such as Boron, at the required temperature and pressure conditions during the test.
Testing to temperatures higher than 500 degrees Fahrenheit can also be undertaken to simulate beyond design basis events.
Different sizes of chambers are available to accommodate a full range of test items from small to large and in the event the test specimen will not fit into an existing chamber, we can design and build custom chambers.
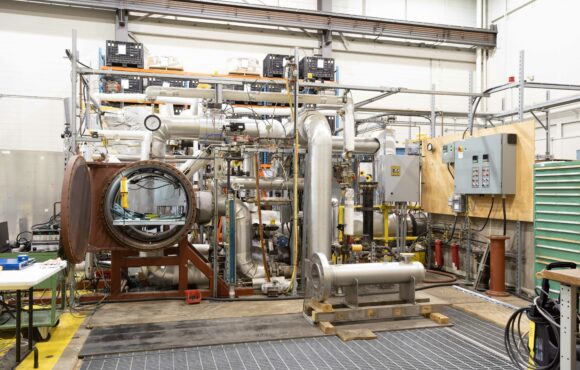
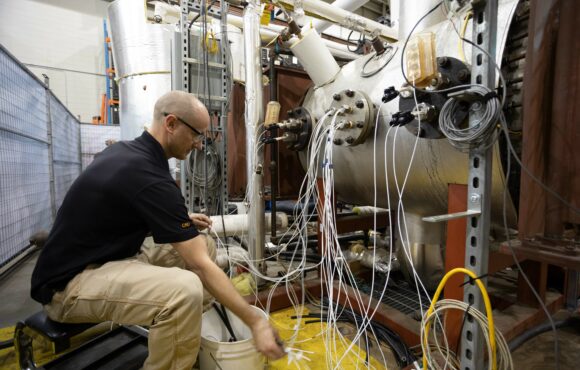
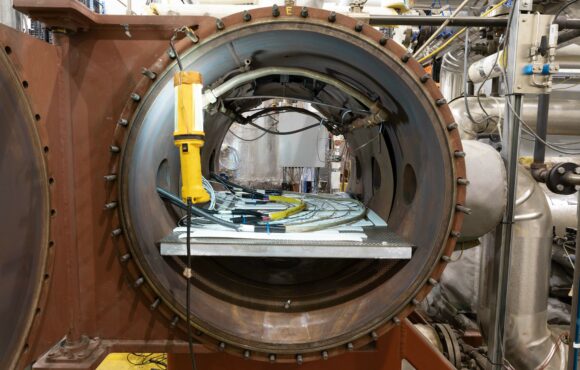
Environmental Chambers
More than 14 ovens and chambers enable us to perform a wide range of temperature and humidity tests. The ovens and chambers vary in size and can accommodate both large and small components. Environmental chamber temperature and humidity are closely controlled to meet specific environmental conditions.
Testing conditions available include:
- Temperatures between -100° F and 1300°F
- Humidity ranges typically between 5% and 95%
- Tracking and recording of temperatures according to required profiles
- Alarm notifications to aid in managing anomalous events, such as loss of power
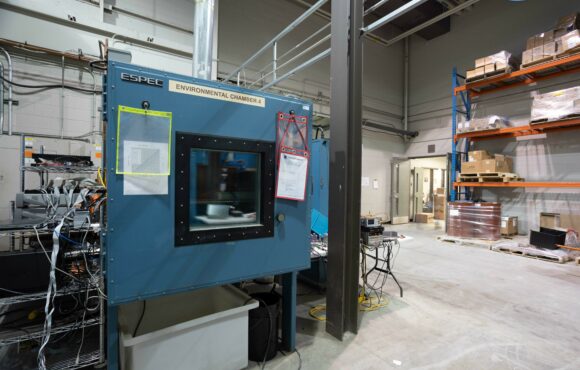
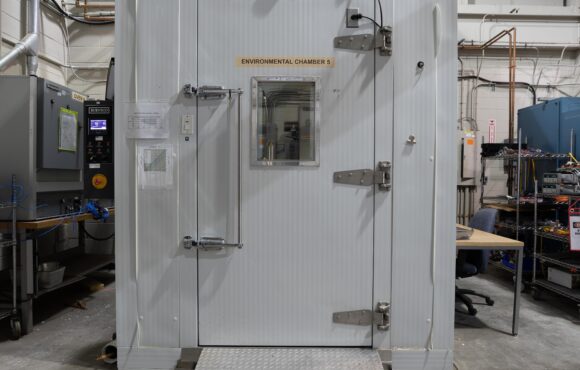
Seismic Testing
Our 3ftX3ft independent tri-axial T-slotted shaker table has a 4,000 lb. capacity, 10-inch stroke actuators, Zero Period Acceleration (ZPA) of 12.0, an overturning moment of 130,000 ft-lbs, and a frequency range greater than 1Hz to 100HZ with a peak sinusoidal velocity of 50 in/sec. Additional key statistics include:
- Motion in 3 directions with minimal coherence between axes
- "Easy-To-Read" single-page presentation of the tri-axial test results
- Random, sine-sweep, or continuous sine-wave excitation
Our single-axis, hydraulic actuated, Random Input Motion (RIM) Table has a displacement limit of 10 inches and a frequency range greater than 1Hz to 100HZ. It has a peak sinusoidal velocity of over 50 in/sec and a payload capacity of 24,000 lbs with a ZPA of 1g or 6000 lbs with a ZPA of 8g.
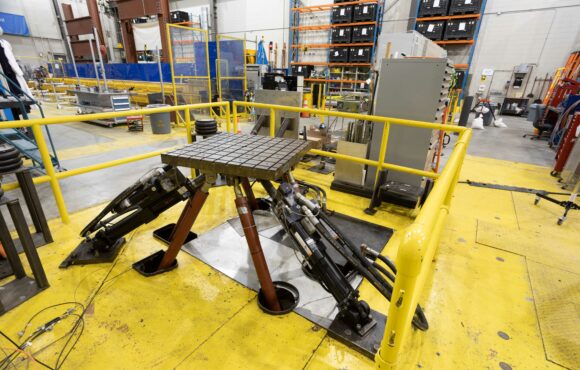
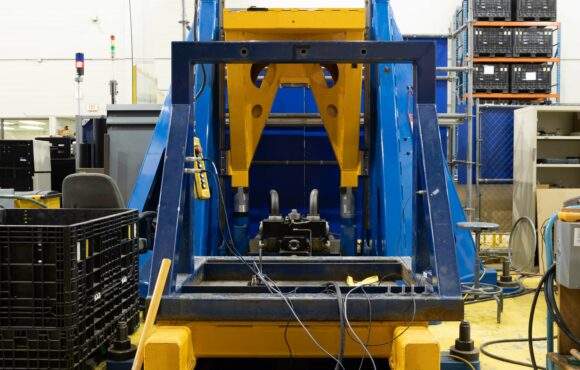
Burst Test Facility
Our burst test containment facility has a maximum internal pressure of 245 kpa (35.5 psi) and maximum temperature of 100 °C and can accommodate a range of other service conditions. It can be used to validate models and to demonstrate actual structural limits. This facility is often used to demonstrate structural integrity and design margins of steam generators and feeder pipes through burst testing of components containing engineered flaws.
The Containment Room Pressure Limits are:
- Maximum Internal Pressure 245 kpa (35.5 psi)
- Maximum Internal Temperature 100 °C
- Energized Test Structure 10.5 kg (23 lb) of TNT equivalent
The Reaction Floor Main Beams can deliver:
- Axial Tensile Force of up to 1250 tonnes
- Maximum Bending Moment of 7700 kN.m (5700 kip ft.)
- Maximum Shear of 2200 kN (500 kip)
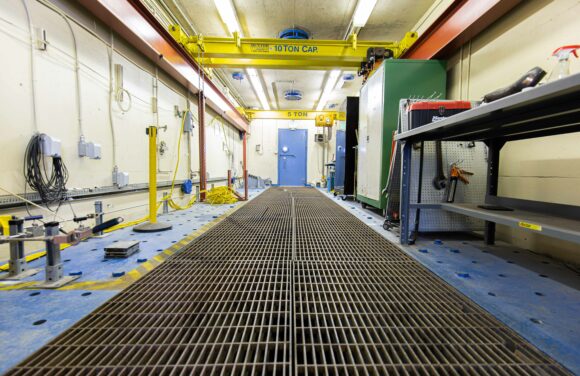
Autoclaves for Corrosion Testing
We have a 7.5 liter autoclave with a maximum pressure of 1900 PSI and a maximum temperature of 350 degree C and a 1.8 liter autoclave with a maximum pressure of 5,000PSI at up to 500 degree C, enabling us to simulate most reactor conditions.
Irradiated Materials Testing Facilities
Working with our partners, McMaster University and the Korean Atomic Energy Research Institute, we operate or have access to facilities that enable us to prepare samples from activated materials and then undertake tests. These facilities include:
Our joint Kinectrics/McMaster Material Preparation and Specimen Machining Facility includes:
- A capability to hydride irradiated pressure tube sections to elevated hydrogen levels
- The ability to machine specimens using an EDM or CNC mill
- The ability to precisely machine notches using a CNC mill
An Irradiated Fatigue and Overload Test Facility that includes:
- A specially developed mechanical test system equipped with an uninterruptible power supply (UPS) that enables us to perform long load-rise time fatigue tests and overload tests on miniature specimens
Our Joint Kinectrics/KAERI Irradiated Burst Test Facility that includes:
- The ability to undertake a burst test on full-scale irradiated Zr-Nb pressure tube specimens to measure the fracture toughness
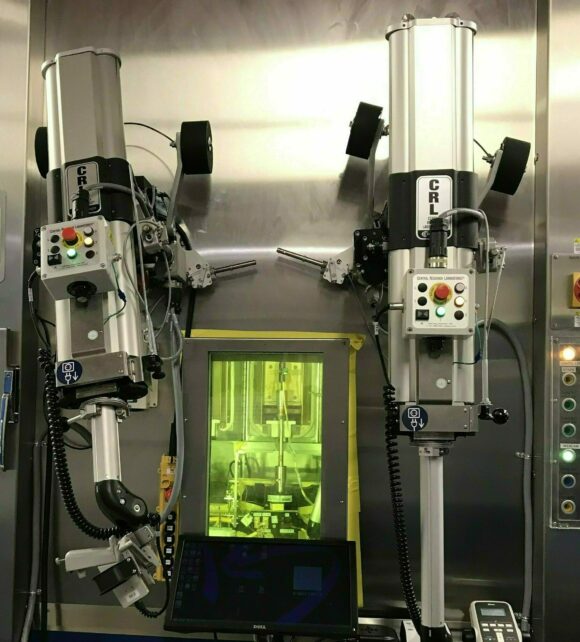
Mock-up Testing and Rehearsal Facility
During operation many key components of a nuclear reactor are inaccessible and even during an outage access may be restricted both by the physical layout and the high radiation fields. To ensure that everything goes to plan, station operators are using mock-ups to enable equipment to be tested and for the deployment team to hone their skills. This approach maximizes the likelihood of a critical path project being completed on time and minimizes the radiation dose to operatives.
Our mock-up and rehearsal facility enables us to test equipment and train deployment teams in a comfortable environment.
The facility benefits from being at the heart of our campus and is supported by other technical teams who can design and build the mock-up, modify, and improve tools and provide advice on radiation protection and human factors.
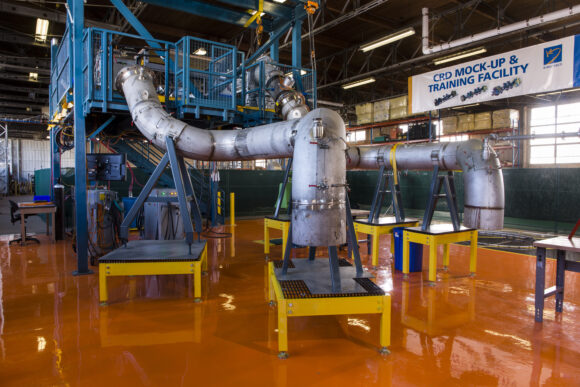